Acid tin plating is a specialized electroplating process that deposits a thin layer of tin onto various metal substrates. Renowned for producing bright, uniform, and corrosion-resistant coatings, acid tin plating plays a crucial role in numerous industrial applications. This method leverages phenolsulfonic acid as a key electrolyte component, ensuring optimal plating quality and performance. This article delves into the intricacies of acid tin plating, exploring its methodology, applications, advantages, and future prospects.
The Acid Tin Plating Process
Electrolyte Composition
At the heart of acid tin plating lies the electrolyte solution, predominantly composed of phenolsulfonic acid. This acid serves as the primary electrolyte, facilitating the efficient deposition of tin ions onto the substrate. The typical composition of the electrolyte includes:
• Phenolsulfonic Acid: Acts as a stabilizer and complexing agent, ensuring a consistent tin ion concentration.
• Tin Salts: Provide the necessary tin ions (Sn²⁺) for deposition.
• Additives: Enhance brightness, leveling, and throwability of the tin coating.
Plating Mechanism
The acid tin plating process involves immersing the metal substrate into the electrolyte solution. An electric current is applied, prompting tin ions to migrate towards the substrate’s surface. The controlled reduction of these ions results in the formation of a dense, adherent tin layer. Key parameters influencing the process include:
• Temperature: Typically maintained between 40°C to 60°C to optimize plating efficiency.
• Current Density: Carefully regulated to ensure uniform deposition without defects.
• pH Levels: Maintained to stabilize the electrolyte and prevent unwanted side reactions.
Surface Preparation
Effective acid tin plating demands meticulous surface preparation to ensure optimal adhesion and coating quality. This involves:
1. Cleaning: Removal of contaminants, oils, and oxides from the substrate using degreasers and acidic or alkaline cleaners.
2. Activation: Treating the surface with activators to enhance tin ion adsorption.
3. Rinsing: Ensuring the substrate is free from residual chemicals before immersion in the electrolyte.
Applications
Acid tin plating is versatile, finding utility across various industries due to its ability to provide superior coating qualities. Notable applications include:
Electronics and Electrical Components
Tin coatings are integral in electronic manufacturing, offering excellent solderability and protection against oxidation. Acid tin plating ensures that connectors, circuit boards, and other components maintain reliable electrical connections and prolonged lifespans.
Automotive Industry
In automotive manufacturing, acid tin plating is employed to coat critical components such as connectors, sensors, and electronic modules. The bright, uniform tin layers enhance both aesthetic appeal and functional durability, resisting corrosion in harsh environmental conditions.
Decorative Finishes
Tin-plated surfaces are favored for decorative purposes in household appliances, hardware, and consumer electronics. The bright finish achieved through acid tin plating elevates product appearance while providing a protective barrier against wear and tear.
Food Packaging
Tin coatings are used in food packaging materials, particularly in cans and containers. Acid tin plating ensures that the inner surfaces are non-toxic, corrosion-resistant, and compliant with food safety standards, preserving the quality and safety of packaged goods.
Advantages of Acid Tin Plating
Enhanced Corrosion Resistance
Tin’s inherent resistance to corrosion makes acid tin plating ideal for protecting metal substrates from environmental degradation. This attribute is crucial in applications exposed to moisture, chemicals, and varying temperatures.
Superior Adhesion and Uniformity
The use of phenolsulfonic acid as an electrolyte ensures that tin deposits adhere strongly to the substrate, forming a uniform and defect-free coating. This uniformity is essential for both functional performance and aesthetic quality.
Improved Solderability
In electronics, the tin layer provides an excellent surface for soldering, facilitating reliable and efficient connections. This is particularly important in high-density circuitry where precise and consistent solder joints are paramount.
Aesthetic Appeal
The bright finish achieved through acid tin plating enhances the visual appeal of products. This is especially beneficial in consumer-facing applications where appearance can influence purchasing decisions.
Limitations and Considerations
Environmental and Safety Concerns
The use of phenolsulfonic acid and other chemicals in the plating process necessitates stringent environmental and safety measures. Proper handling, disposal, and recycling of electrolyte solutions are essential to minimize environmental impact and ensure workplace safety.
Cost Implications
While acid tin plating offers numerous benefits, the costs associated with high-purity chemicals, energy consumption, and process control can be higher compared to other plating methods. Balancing quality requirements with budget constraints is a critical consideration for manufacturers.
Substrate Compatibility
Not all metals are equally compatible with acid tin plating. Pre-treatment and surface preparation are crucial to ensure optimal adhesion and coating quality, especially when dealing with substrates that form passive oxides or have irregular surfaces.
Future Trends in Acid Tin Plating
Advancements in Electrolyte Formulations
Ongoing research aims to develop more efficient and environmentally friendly electrolyte formulations. Innovations may include alternative complexing agents that reduce environmental impact while maintaining or enhancing plating performance.
Automation and Process Control
The integration of advanced automation and real-time monitoring systems is set to revolutionize acid tin plating. Enhanced process control can lead to higher consistency, reduced defects, and improved overall efficiency.
Sustainable Practices
With increasing emphasis on sustainability, the industry is exploring methods to recycle and reuse plating solutions, reduce waste, and minimize energy consumption. These practices not only benefit the environment but also offer cost savings and compliance with regulatory standards.
Nanotechnology Integration
Incorporating nanotechnology into acid tin plating could lead to the development of coatings with superior properties, such as increased hardness, enhanced wear resistance, and improved electrical conductivity. This integration holds promise for high-performance applications in cutting-edge industries.
Conclusion
Acid tin plating stands as a pivotal process in the realm of metal finishing, offering a blend of aesthetic excellence and functional durability. By leveraging phenolsulfonic acid as an effective electrolyte, manufacturers can achieve bright, uniform tin coatings that enhance the performance and appearance of a wide range of products. As the industry evolves, advancements in technology and sustainable practices will continue to refine and expand the applications of acid tin plating, cementing its role in modern manufacturing and industrial processes.
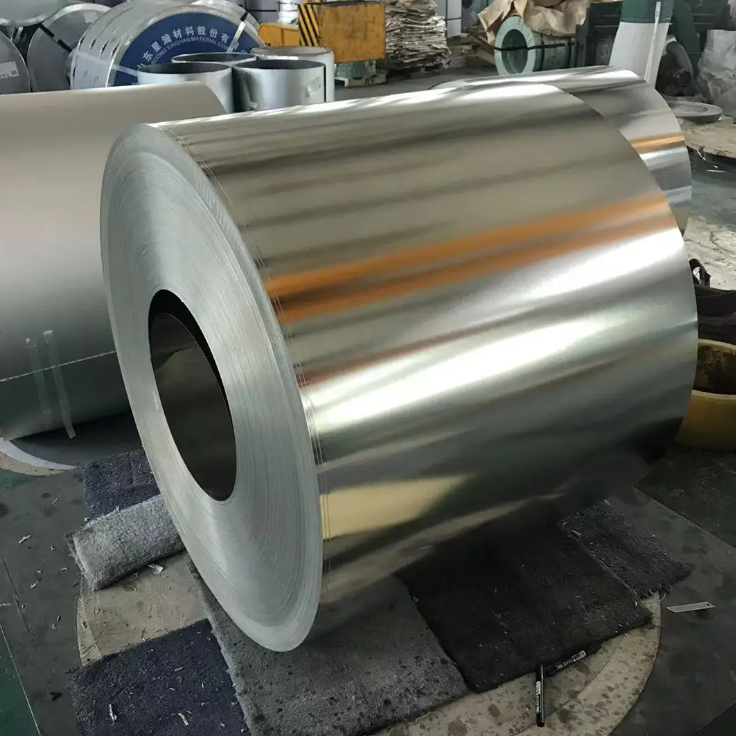
About Taihua
Taihua Chemical is a leading supplier of high-purity Phenolsulfonic Acid, catering to the diverse needs of the textile industry. With a focus on quality and reliability, we support our clients in achieving optimal dye fixation and superior fabric performance. For more information, visit this page please.